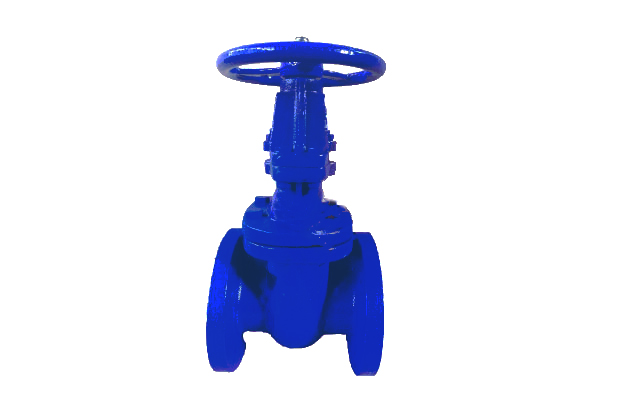
The valves disc is rubber-packed to get excellent sealing effect by the rubber's resilient deformation. Non-rising resilient seated gate valves solve the problem in general gate valves such as leakage, rusting etc. and saves installation space. It is used widely in tap water industry, sewage treatment, shipping construction, petroleum, chemicals, food, pharmacy, textile, electric power, metallurgy and energy system's pipeline to adjust and shut off fluids.
Body Material: Cast Iron GG25, Ductile Iron GGG40, GGG50
Disc Materials: Cast Iron GG25, Ductile Iron Coated with EPDM/NBR
Sealing Material: Brass, Bronze
Stem Materials: Carbon Steel, Stainless Steel 416, Stainless Steel 304, Brass, Bronze
Bolt: Carbon Steel, Stainless Steel 304, Stainless Steel 316
Cover: Cast Iron GG25, Ductile Iron GGG40, GGG50
Thrust Bearing: Brass
Gland: Cast Iron GG25, Ductile Iron GGG40, GGG50
Hand Wheel: Cast Iron GG25, Ductile Iron GGG40, GGG50
End Connection: Flanged
1.The seal is designed with dustproof ring plus three “O”-seal ring, reliable sealing, on-line replaceable.
2.Both gate and aluminum bronze bearing are in inside design good self lubrication ,high strength and can have the aluminum bronze bearing replaced without need to replace the gate integrally, after a long time use.
3.Rubber wrapped gate anti-corrosion, good tightness.
4.Advanced surface treatment, coated with non-toxic epoxy resign static powder, anti-corrosion, pollution-free, can be used drinking water pipeline.
5.The body is designed without gate slot, the smooth passage will not get impurities filling up, more applicable for sewage working condition.
6.The integral seal works reliably. For the high pressure seal, leaving zero leakage under 1.5 times nominal pressure and, for the low pressure one, under 0.02Mpa.
Bolted Bonnet
Replaceable O-ring
Rubber encapsulated wedge, Brass Wedge Nut.
Fusion bonded epoxy coated inside and outside, blue RAL 5017 200 Micron think.
Working pressure from -1 to +16 bar and working temperature from -10 to +80℃
DN | L | D | D1 | b | n-d | w | Fl(open) |
50 | 177.8 | 152 | 120.7 | 15.9 | 4-φ19 | 178 | 375 |
65 | 190.5 | 178 | 139.5 | 17.5 | 4-φ19 | 178 | 408 |
80 | 203.2 | 190 | 152.5 | 19.1 | 4-φ19 | 190 | 442 |
100 | 228.6 | 229 | 190.5 | 23.9 | 8-φ19 | 250 | 545 |
125 | 254 | 254 | 216 | 23.9 | 8-φ22 | 300 | 656 |
150 | 266.7 | 279 | 241.5 | 25.4 | 8-φ22 | 356 | 770 |
200 | 292.1 | 343 | 298.5 | 28.6 | 8-φ22 | 400 | 959 |
250 | 330.2 | 406 | 362 | 30.2 | 12-φ25 | 457 | 1255 |
300 | 355.6 | 483 | 432 | 31.8 | 12-φ25 | 508 | 1443 |
1.Design and manufacture according to ANSI B16.1 Class 125/Class 150
2. Face to face according to ANSI B16.1 Class 125/Class 150
3.Flange drilling according to ANSI B16.1 Class 125/Class 150
4.Pressure test according to MSS SP-70